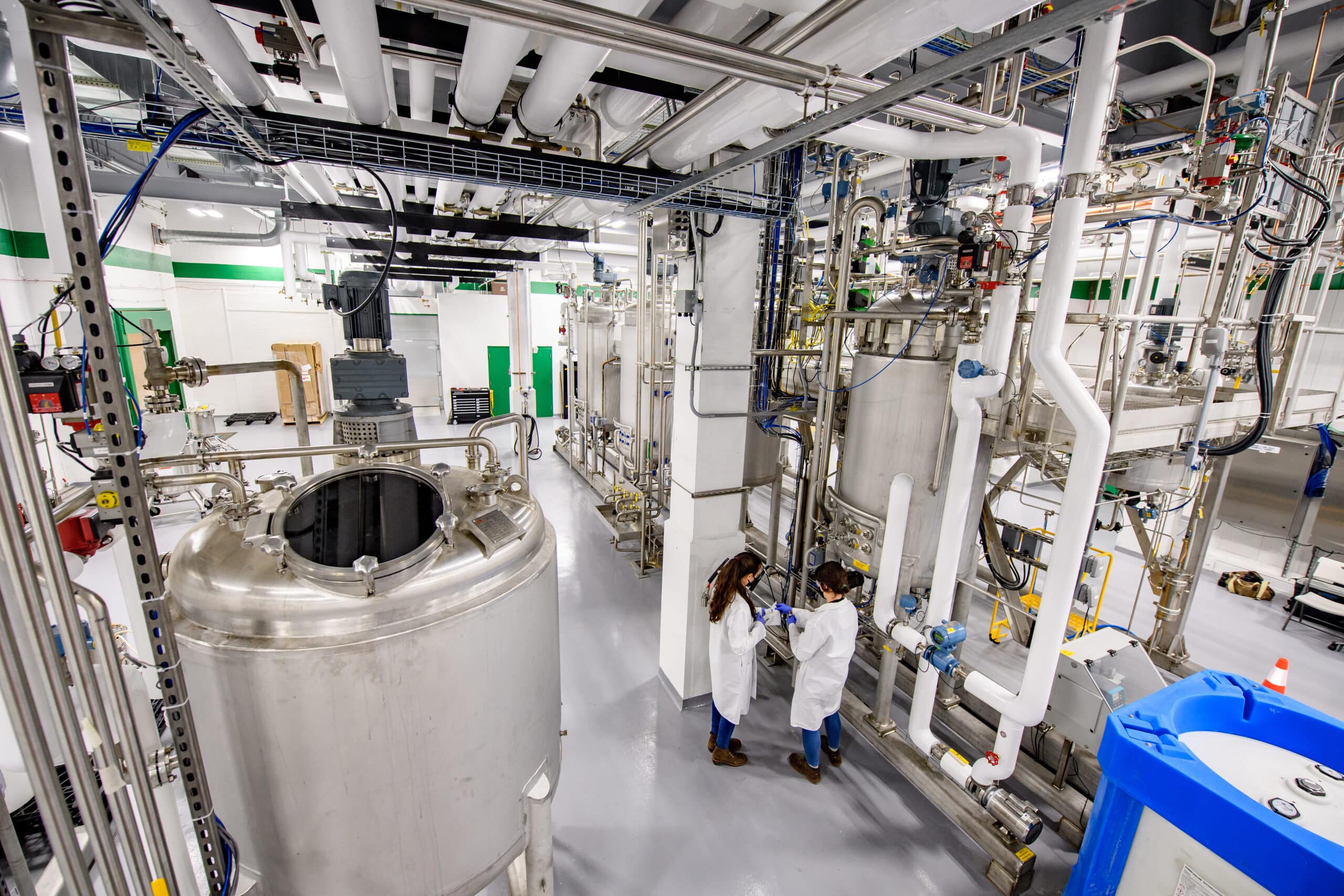
Como escalar a produção de RNA
A arte e a ciência de levar a receita de aumento de escala de RNA do laboratório para uma fábrica
“Há uma diferença entre assar um pão normal e um pão gigantesco 10.000 vezes maior”, diz Adam Shanebrook, biotecnólogo e diretor de planta piloto da GreenLight Biosciences. “Você queimará o exterior e deixará o interior cru.” Seu argumento: você não pode simplesmente ampliar os processos químicos e biológicos. Você tem que ser inteligente sobre isso.
Isso está muito na mente dos pesquisadores da GreenLight, pois eles ampliam a fabricação de laboratório para a produção comercial de suas soluções baseadas em RNA voltadas para besouros da batata do Colorado, uma praga agrícola e ácaros varroa, que dizimam colônias de abelhas. Foi demonstrado que a síntese inovadora de RNA livre de células da empresa funciona em escala de laboratório há alguns anos em Medford, Massachusetts, mas a GreenLight abriu um planta piloto em uma antiga fábrica da Kodak em Rochester, Nova York para fazê-lo funcionar em uma escala muito maior.
A produção de RNA em um laboratório ou fábrica normalmente envolve a edição de genes de uma célula, geralmente uma bactéria inofensiva. Mas o processo não fabrica apenas RNA, ele também produz o resto da bactéria. Isso significa que está desperdiçando muita energia e matéria-prima na fabricação de subprodutos indesejados. Além disso, esses subprodutos são misturados ao RNA que você realmente deseja, então você precisa separá-los — um processo caro e difícil — ou lidar com um produto final impuro, cheio de detritos que sobraram das células.
O processo livre de células
O processo livre de células funciona de forma bem diferente. Ele usa cepas inofensivas de Escherichia coli—usado há muito tempo na indústria farmacêutica para produzir coisas como insulina humana—para fazer os materiais de partida para a reação livre de células. Para se preparar para isso, anéis curtos de DNA chamados “plasmídeos” são feitos para fornecer instruções de montagem para a etapa de produção de RNA livre de células. Além disso, Escherichia coli são usados para fazer as enzimas que catalisam a produção e montagem da molécula de RNA.
Em seguida, esses produtos são colocados em uma grande cuba contendo uma “sopa” de nucleosídeos, os blocos de construção do RNA e do DNA, e as enzimas retiram os nucleosídeos flutuantes da sopa, os energizam para que se encaixem como ímãs e os montam em uma linha de acordo com as instruções dos plasmídeos de DNA. Isso tem a vantagem de ser mais rápida do que a produção de células bacterianas — talvez 10 vezes mais rápida, exigindo cerca de três horas por lote, em vez de cerca de 30; é mais barata; e produz um produto muito mais puro, aproximadamente 50-65% puro.
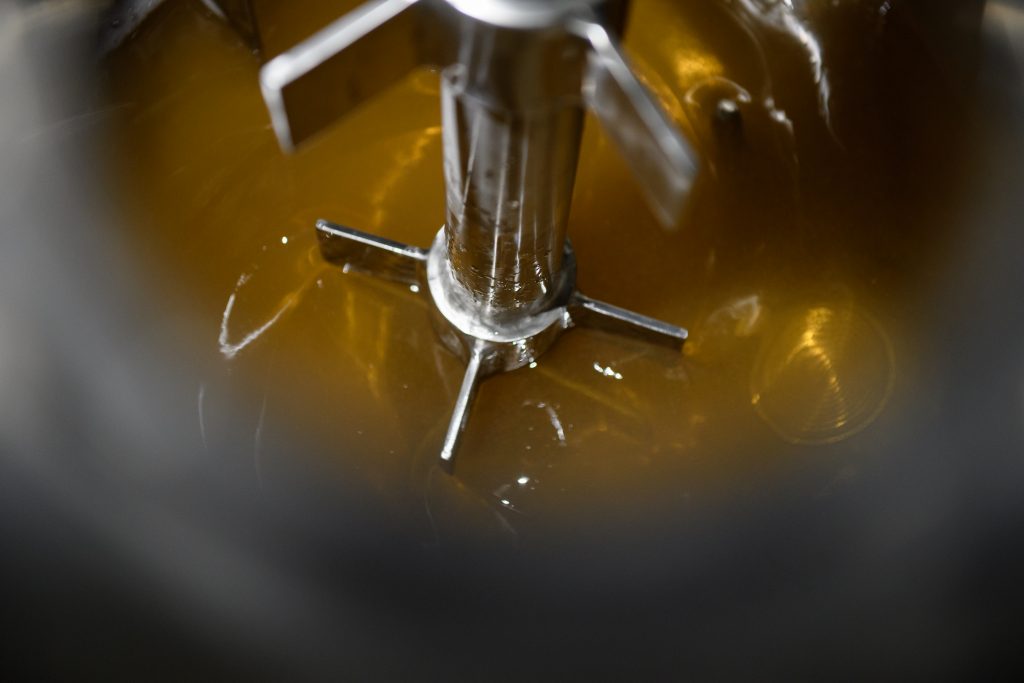
Em 2017, foi demonstrado que tudo funcionava no laboratório. Mas, embora possa ser fácil fazer uma baguete de 8 polegadas em um forno doméstico, isso não significa que você poderia fazer com sucesso um pão de 65 pés de comprimento em um gigantesco megaforno.
Construindo um reator de até 1.250 litros
Karthik Ramachandriya é engenheiro bioquímico e diretor de desenvolvimento de processos na GreenLight. Ele segura um objeto pequeno, do tamanho de uma tampa de caneta. “Os primeiros experimentos foram feitos em um reator de 50 microlitros”, diz ele — ou seja, 0,05 mililitros, uma quantidade pouco visível. “Em seguida, aumentamos isso para 250 ml.” Ele segura uma xícara de café. “Não foi tão desafiador passar de um microrreator para uma xícara de café.” Em seguida, a equipe testou em um reator de bancada que continha 10 litros. Finalmente, em 2019, a empresa começou a construir a fábrica de Rochester, testando um reator de 150 litros e, eventualmente, um de 1.250 litros.
“Descobrimos como fazer tudo isso em escala de bancada em Medford”, diz Eric Otto, biotecnólogo e vice-presidente de fabricação da GreenLight. Mas em ambos os estágios — produzir os plasmídeos e enzimas e produzir o RNA — houve desafios associados ao aumento de escala.
Com a produção de enzimas e plasmídeos, “nosso público-alvo era o bom Escherichia coli que estamos tentando fazer feliz”, diz Otto. “É como fazer cerveja, mas um pouco mais complicado. Você precisa manter o que o organismo precisa e fornecer oxigênio e outros nutrientes suficientes enquanto remove o dióxido de carbono para que a fermentação não adoeça.”
Mas manter essas condições é um trabalho diferente em um tanque de 150 litros do que em um de um litro. “No laboratório, você o agita em um tubo”, diz Shanebrook. “Mas em uma fábrica, você não pode simplesmente sacudi-la quando se trata de um tanque inteiro.”
“A mixagem é diferente”, concorda Erin Cobb, engenheira de processo. “Não é mais instantâneo. Não é perfeitamente uniforme. A forma como você está entregando oxigênio às células é diferente; é fácil em pequena escala usar oxigênio engarrafado, mas isso não é econômico quando você aumenta a escala e é um risco de combustão, então você precisa usar ar pressurizado.” Você pode simplesmente agitar um frasco de um litro para levar todos os nutrientes para onde eles precisam estar, e tudo estará automaticamente em uma temperatura uniforme.
Bombas, empilhadeiras e correias transportadoras
Cobb acrescenta que também há problemas logísticos. Se você está adicionando um quilo de sal a um reator, ela diz: “Eu posso levantar isso com minha mão. Posso fazer isso com algo 10 vezes maior? Eu posso pegar o tanque de 10 litros e despejá-lo fora; eu não posso com o de 1.000 litros. Preciso de bombas, empilhadeiras, correias transportadoras.”
Até tarefas prosaicas, como a limpeza, se tornam mais complicadas. “A espátula com a qual coloquei a matéria-prima no pequeno tanque”, diz ela: “Posso levá-la até a pia e lavá-la na autoclave”, uma máquina que esteriliza equipamentos com vapor. “Você não pode colocar um tanque de 1.000 litros em uma autoclave. Você precisa de um sistema totalmente estéril, precisa aquecê-lo a 120° C, precisa de ar esterilizado entrando no sistema.”
Também há um problema de recursos humanos. À medida que o processo se torna maior e depende de muitos outros conjuntos de habilidades, você precisa de diferentes tipos de mão de obra. A instalação da fábrica de Rochester foi um bom exemplo. “Você precisa saber sobre serviços públicos, alarmes de incêndio, sprinklers, aquecimento, ventilação e drenos de piso”, diz Shanebrook. “Você está lidando com centenas de pessoas em profissões especializadas. Pessoas que consertam o telhado, revestem o chão.”
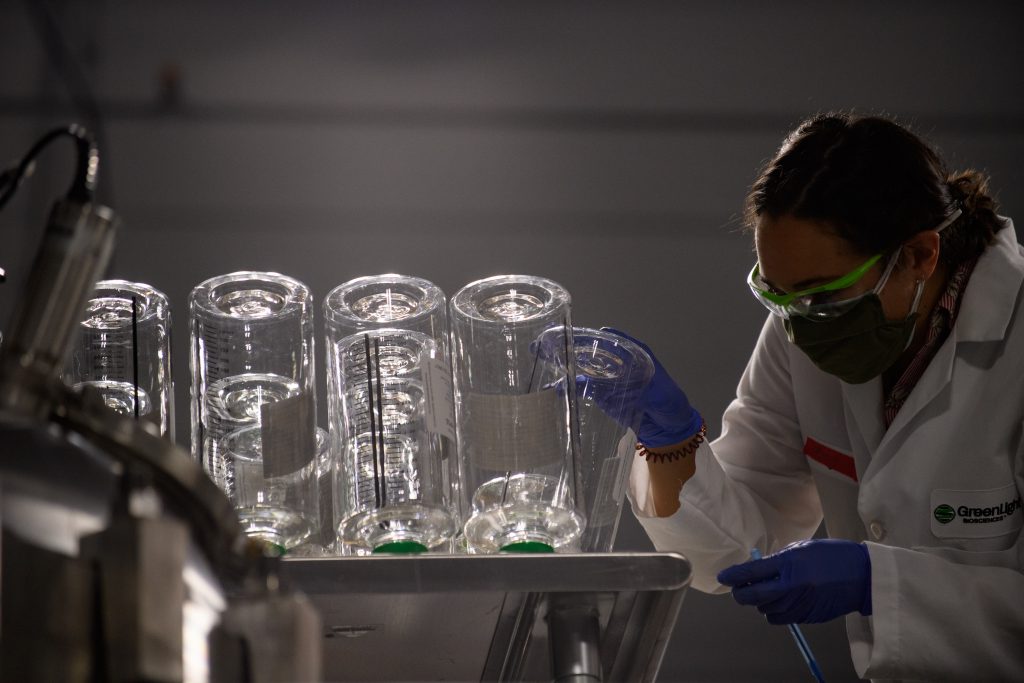
Dentro da própria GreenLight, existem muitas marcas de especialização — engenheiros, biotecnólogos, químicos, entomologistas, agrônomos — todas as quais precisam entender a especialidade umas das outras até certo ponto. “O mais importante ao aumentar e reduzir a escala é entender as pessoas que trabalharam no processo e se sentir realmente à vontade para fazer perguntas”, diz Cobb. “Posso ligar a qualquer hora e perguntar: isso parece estranho? Deveria ter essa aparência?”
Uma planta que pode crescer
Há outras complicações. Embora a fábrica de Rochester seja uma grande fábrica de RNA direcionada, ela própria é um piloto para uma instalação muito maior — centenas de vezes maior, 20.000 litros ou mais. Portanto, não adianta resolver um problema em uma escala de 150 litros se ele não funcionasse em uma escala muito maior. Por exemplo, pode ser fácil encontrar maneiras de remover resíduos de um tanque de um litro, para que as bactérias possam prosperar. Mas, a menos que a solução também funcione em uma escala muito maior, ela não é uma solução. A planta piloto foi projetada, na medida do possível, para imitar a realidade de uma planta comercial maior. “Você precisa entender as limitações de um reator de 20.000 litros quando estamos desenvolvendo um processo em um reator de um litro”, diz Ramachandriya.
“Este é o nosso playground”, diz Shanebrook. “Na planta comercial, ela será projetada para o propósito: sua bomba vai de A a B, é dedicada a essa função.
“Mas na planta piloto, você não sabe do que precisa e precisa aceitar isso. Você precisa ser flexível, usar mangueiras que vão de A a B, de A a C ou de D a A. Você aceita as mudanças com calma.”
Quando você encontra um problema na planta piloto, diz Ramachandriya, o importante é voltar às escalas menores e entendê-lo adequadamente. “Se for uma função biológica, voltamos à escala minúscula”, diz ele. “Se for uma função de processo, fazemos isso na xícara de café ou no tamanho de um litro.” Se o seu Escherichia coli estão infelizes e produzem muito ácido, você provavelmente pode explicar isso no microrreator. Se seus tubos estiverem entupindo porque a solução de RNA fica muito viscosa, você precisará de reatores maiores, com seus próprios tubos e bombas, para ver onde está errado.
O reator da GreenLight energiza nucleotídeos
O que também é importante à medida que você aumenta a escala, diz Ramachandriya, é manter os custos baixos. Por exemplo, quando você está pedindo milhares de litros de solução de nucleotídeos ou nutrientes para o seu Escherichia coli, você não quer gastar muito por litro. Os nucleotídeos são feitos de subprodutos de levedura e energizados por enzimas no próprio reator da GreenLight; eles podem ser comprados a granel. “A indústria de leveduras é muito grande e produz uma variedade de produtos a partir de seu processo especializado, e nós ganhamos com as economias de escala”, diz Otto.
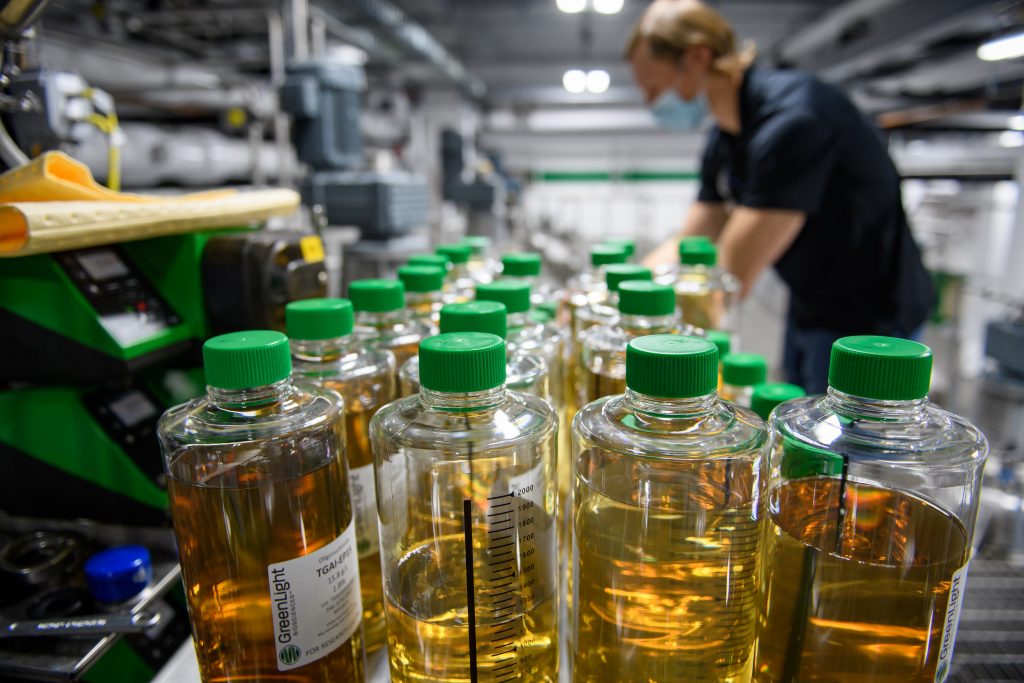
Shanebrook acrescenta que o projeto de escalonamento ainda não foi concluído. É preciso prever a demanda futura: se, como espera a GreenLight, seus produtos se tornarem amplamente utilizados, mesmo o reator planejado de 20.000 litros não será suficiente. “É ler as folhas de chá e planejar a expansão”, diz ele. “Como fabricante, você não quer ser a etapa limitante. Se o lado comercial disser: 'Queremos uma fábrica maior', você quer poder dizer: 'Temos um plano para isso'; é um problema comum que as empresas digam que queremos isso no próximo mês, e os tecnólogos digam que levará dois anos.”
Em algum momento, aumentar ainda mais a escala em uma única planta se torna impossível. “Na panificação”, diz Shanebrook, retornando à sua metáfora anterior, “às vezes você alcança uma escala, número X de toneladas, onde não pode mais aumentar a escala. Em vez disso, você aumenta o número.” Ou seja, você constrói mais plantas, fazendo a mesma coisa. Tem vantagens de redundância em caso de desastre.
O GreenLight ainda não está nesse estágio. Mas Shanebrook, em particular, já está pensando em maneiras de continuar o processo de aumento de escala. No momento, em cada escala — seja de 50 microlitros ou 1.250 litros — o RNA é produzido em lotes: um reator é preenchido com matéria-prima, deixado para funcionar e o produto final é colhido. Mas talvez o futuro seja a produção contínua: “Você pode colocar tudo isso na panela de sopa por três horas”, diz ele, “ou pode ter um cano longo que leva três horas para fluir da entrada para a saída”.
A capacidade de correr continuamente é um cenário para o futuro, ele espera. Mas o aumento de escala já foi espetacular, atingindo centenas de milhares de vezes o volume que a equipe da GreenLight fez há apenas alguns anos.
“É como se eu me sentasse com os chefs da casa”, diz Cobb, “e depois aprendesse a organizar o casamento”.